Das Einschmelzen von Schrotten geringer Packungsdichte im Mittelfrequenz-Induktionstiegelofen
Frank Donsbach, Steffen Niklaus, Georg Renftle
Der Mittelfrequenz-Induktionstiegelofen hat sich zum Standardaggregat für das elektrische Schmelzen von Gusseisen entwickelt und dabei den Netzfrequenzofen weitestgehend abgelöst. Auch Stahlgießereien und Microstahlwerke setzten immer häufiger Induktionsöfen zum Schmelzen ein. Das direkte Erwärmungsprinzip des induktiven Schmelzens ist metallurgisch vollständig neutral, energieeffizient und umweltfreundlich.
Beim Schmelzen liegt der NOx-Ausstoß unterhalb der Messbarkeitsschwelle und einen CO2-Ausstoß gibt es ebenfalls nicht, insofern der Ofen mit Strom aus erneuerbaren Energien gespeist wird. Die heute verfügbare Leistungselektronik ermöglicht es, den Ofen mit einer für das Schmelzgut optimalen Frequenz zu betreiben. Dabei gilt: Je höher die Frequenz des elektromagnetischen Feldes ist, desto geringer ist die elektromagnetische Eindringtiefe und somit nehmen auch kleine Raumvolumina eines leitfähigen Gutes ausreichend viel Leistung auf. In der praktischen Umsetzung haben sich Frequenzen um die 250 Hz für das Schmelzen von Stahl und Gusseisen als vorteilhaft erwiesen. Bei 250 Hz werden schon in „faustgroßem“ Stückgut ausreichend starke Wirbelströme induziert, um das Material zu schmelzen.
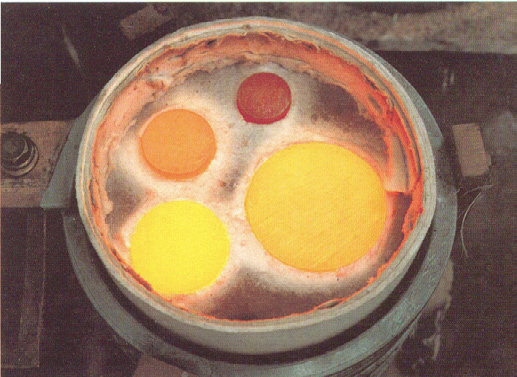
Bild 1: Einfluss der Stückigkeit des Einsatzmaterials auf den Wirkungsgrad der induktiven Energieübertragung (Quelle: RWE)
Bild 1 verdeutlicht den zuvor genannten Sachverhalt anhand eines einfachen Versuchs: In eine Induktionsspule wurden metallische Zylinder verschiedenen Durchmessers eingebracht und mit Sand hinterfüllt, anschließend wurde die Spule bei gegebener Frequenz mit Leistung beaufschlagt. Nach geraumer Zeit zeigt sich, dass die Zylinder eine unter- schiedliche Temperatur aufweisen; der zweitgrößte Zylinder ist am wärmsten. Bei diesem passen offenbar Stückigkeit und Frequenz am besten im Hinblick aus den Wirkungsgrad der induktiven Energieübertragung.
- Aufgrund der besseren elektromagnetischen Ankopplung bei festem (kaltem) Einsatzmaterial aus Eisenwerkstoffen spart die Mittelfrequenzanlage im Gegensatz zum Netzfrequenzofen ca. 5% Energie, da bis zum Erreichen der Curietemperatur ein deutlich höherer Spulenwirkungsgrad anzusetzen ist.
- Es wird keine Energie für das Warmhalten des Sumpfes verbraucht.
- Die Ofengröße kann mindestens um die Sumpfmenge reduziert werden, was Anschaffungs- und Betriebskosten reduziert.
- Legierungswechsel sind einfacher möglich, da der Ofen bei jedem Abguss komplett entleert wird.
- Sollte das Einsatzgut trotz der zwingend erforderlichen Trockenlagerung noch Wasser und Eiseinschlüsse aufweisen, so ist die Gefahr einer Wasserdampfexplosion erheblich geringer, wenn man nicht in ein flüssiges Bad chargiert, sondern in einen leeren Ofen oder auf festes Material aufchargiert.
- Sie ist insgesamt tiegelschonender, weil sie die keramische Ofenauskleidung geringeren Temperaturwechseleinflüssen aussetzt.
- Der Sumpf ermöglicht, auch bei sehr sperrigem Einsatzgut noch genügend Material im Ofen zu haben, welches im elektromagnetischen Feld ankoppelt.
- Sehr kleines Einsatzgut wie zum Beispiel Späne lassen sich mit Hilfe der typischen Badbewegung in einem Induktionsofen niedriger Frequenz sehr gut einrühren.
Der Vollständigkeit halber sei auch erwähnt, dass man Netzfrequenzöfen auch im Chargenbetrieb unter Verwendung eines Anfahrblockes betreiben kann. Dies ist aber unüblich, weil energetisch ungünstig. Der Anfahrblock muss ja praktisch zweimal geschmolzen werden und stellt einen zusätzlichen logistischen Aufwand dar.
Da Energieverbrauch, Investitionskosten, Betriebskosten und Flexibilität bei den Legierungen für viele mittelständische Gießereien im Vordergrund stehen, entscheiden sich heutzutage nahezu alle Kunden für Mittelfrequenzofenanlagen im Chargenbetrieb.
Durch die wachsende Verbreitung des Mittelfrequenztiegelofen bei Gusseisen- und Stahlanwendungen entstehen aber auch immer mehr Anwendungsfälle, in denen die Nutzer gänzlich oder teilweise Materialien zur Verfügung haben, die deutlich geringere Packungsdichten aufweisen, als dies vom Ofenbauer empfohlen wird. Seitens der Ofenbauer wird eine möglichst hohe Packungsdichte des Schmelzgutes empfohlen. Für Eisen- oder Stahlschmelzen ist eine Packungsdichte, auch Schüttdichte genannt, von 2 t/m3 der empfohlene Richtwert. Auf diesen Wert beziehen sich auch die Herstellerangaben für Schmelzleistung und Stromverbrauch eines Mittelfrequenztiegelofens.
Der Vollständigkeit halber sei auch erwähnt, dass man Netzfrequenzöfen auch im Chargenbetrieb unter Verwendung eines Anfahrblockes betreiben kann. Dies ist aber unüblich, weil energetisch ungünstig. Der Anfahrblock muss ja praktisch zweimal geschmolzen werden und stellt einen zusätzlichen logistischen Aufwand dar.
Da Energieverbrauch, Investitionskosten, Betriebskosten und Flexibilität bei den Legierungen für viele mittelständische Gießereien im Vordergrund stehen, entscheiden sich heutzutage nahezu alle Kunden für Mittelfrequenzofenanlagen im Chargenbetrieb.
Durch die wachsende Verbreitung des Mittelfrequenztiegelofen bei Gusseisen- und Stahlanwendungen entstehen aber auch immer mehr Anwendungsfälle, in denen die Nutzer gänzlich oder teilweise Materialien zur Verfügung haben, die deutlich geringere Packungsdichten aufweisen, als dies vom Ofenbauer empfohlen wird. Seitens der Ofenbauer wird eine möglichst hohe Packungsdichte des Schmelzgutes empfohlen. Für Eisen- oder Stahlschmelzen ist eine Packungsdichte, auch Schüttdichte genannt, von 2 t/m3 der empfohlene Richtwert. Auf diesen Wert beziehen sich auch die Herstellerangaben für Schmelzleistung und Stromverbrauch eines Mittelfrequenztiegelofens.
Durchgeführte Schmelzversuche
Die Öfen werden mit einer längsverfahrbaren Vibrationsschwingrinne mit einem Fassungsvermögen von 8t) befüllt (Bild 3 und 4). Der Behälter der Schwingrinne für eine Schüttdichte von 1 t/m3 ausgelegt.
- Chargenfahrweise (leerer Ofen), Packungsdichte 2 t/m3
- Chargenfahrweise (leerer Ofen), Packungsdichte 1,3 t/m3
- Chargenfahrweise (leerer Ofen), Packungsdichte 0,5 t/m3
- Sumpffahrweise (1 t Sumpf), Packungsdichte 1,3 t/m3
- Sumpffahrweise (1 t Sumpf) zzgl. 1,5 t Späne
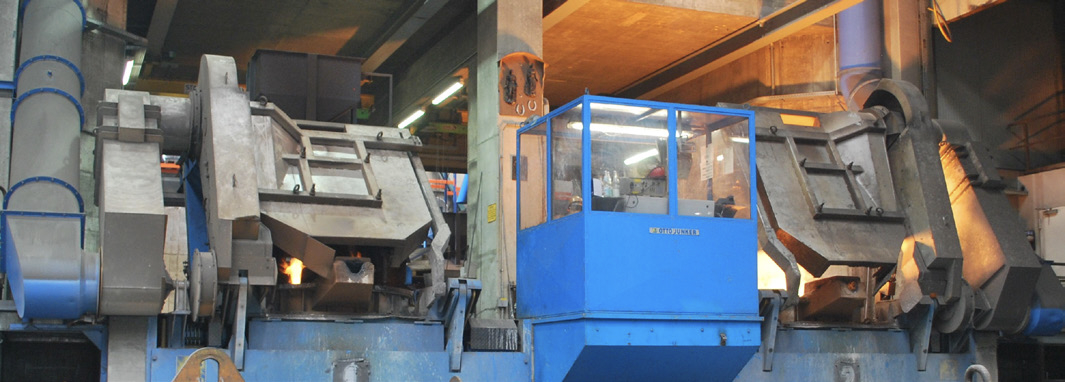
Bild 2: MFT Ge 8000 Duomeltanlage der Eisengießerei Düker in Laufach, Fabrikat Otto Junker
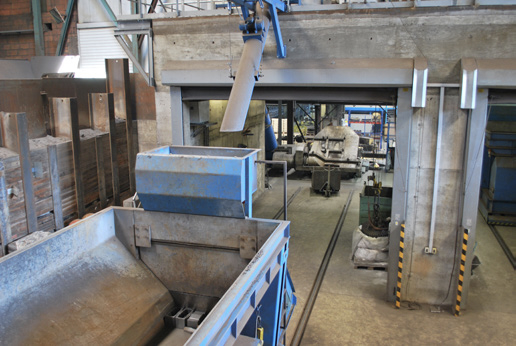
Bild 3: Chargiermaschine im Gattierungsbereich mit Durchfahrt zu den Schmelzöfen
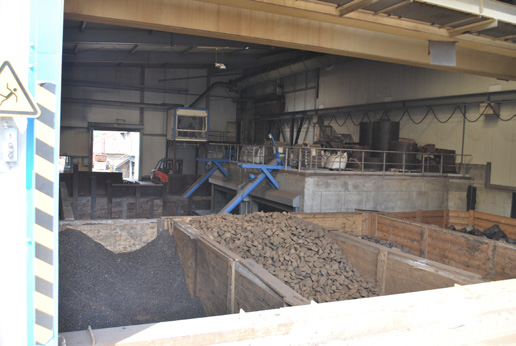
Bild 4: Schrottlager- und Gattierungsbereich bei Fa. Düker, Laufach
Ergebnisse
A). Chargenfahrweise (leerer Ofen) Packungsdichte 2 t/m3
B). Chargenfahrweise (leerer Ofen) Packungsdichte 1,3 t/m3
C). Chargenfahrweise (leerer Ofen) Packungsdichte 0,5 t/m3
D.) Sumpffahrweise (1 t Sumpf), Packungsdichte 1,3 t/ m3
E.) Sumpffahrweise (1t) plus 1,5 t Späne
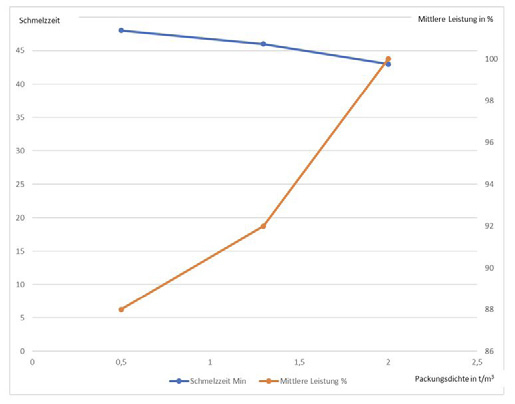
Bild 5: Einfluss der Packungsdichte des Chargiermaterials auf die Schmelzzeit und die mittlere aufgenommene Leistung
Schlussfolgerungen
Der Einfluss der Packungsdichte des Einsatzgutes eines Mittelfrequenz-Induktionstiegelofens auf die Dauer einer Schmelze und somit auf die Schmelzleistung ist nicht unerheblich. Packungsdichten <1 t/m3 stellen kein unüberwindbares Hindernis dar, führen aber bei einem für gute Packungsdichten dimensionierten Ofen zu Einbußen in der Schmelzleistung in der Größenordnung von 10 % und darüber. Die Einschränkungen nehmen jedoch während der Charge mit zunehmendem Ofeninhalt ab. Man kann sagen, dass bei etwa halber Ofengewichtsfüllung oder nach etwa halber Chargenzeit der Einfluss einer geringen Packungsdichte des Einsatzmaterials nicht mehr messbar ist. Falls man sowohl Material guter als auch schlechter Packungsdichte zur Verfügung hat, ist es also empfehlenswert, zuerst das Material mit der höchsten Packungsdichte zu chargieren.
Eine weitere Möglichkeit, den Leistungseinbußen entgegenzuwirken, wäre es, eine Sumpffahrweise mit einem Sumpf von ca. 10-15 % des Ofeninhaltes zu praktizieren. Damit lassen sich nahezu vergleichbare Schmelzzeiten erreichen, wie dies mit Material guter Packungsdichte möglich ist. In diesem Fall muss man natürlich die Nachteile des Sumpfbetriebs wie zum Beispiel die geringere Abgussmenge und die eingeschränkte Flexibilität bei Legierungswechseln und Betriebsunterbre- chungen in Kauf nehmen.
Die erste Einschmelzphase ist in der Regel dadurch gekennzeichnet, dass zeitlich nacheinander die Strom- und Spannungsgrenze des Umrichters über längere Zeiträume erreicht werden, wodurch sich jeweils eine momentane Leistung ergibt, die zumeist unter der Nennleistung liegt. Um hier im Einzelfall, zum Beispiel bei Verwendung ungünstiger Schrotte, eine Leistungserhöhung zu erwirken und somit die Gesamtschmelzzeit zu verkürzen, kann die Auslegung der elektrischen Parameter und der Umrichteranlage so erfolgen, dass größere Strom und Spannungsreserven zur Verfügung stehen. Faktisch würde man hinsichtlich der Leistungshalbleiter dann zum Beispiel eine 8 MW Anlage wie eine Anlage für 10 MW dimensionieren. Die übrigen Komponenten wie zum Beispiel der Transformator und die Rückkühlanlage blieben nach wie vor für 8 MW ausgelegt. Dabei würde dafür Sorge getragen werden, dass die Anlage bei guter Packungsdichte und nach Fortschreiten der Chargierung in ihrer Leistungsaufnahme begrenzt werden kann, auch um zum Beispiel auch Leistungsverfügbarkeiten des Stromversorgers nicht zu überschreiten. Für eine solche Drosselung eignen sich besonders Parallelschwingkreisumrichter in IGBT Technik, da bei diesen Umrichtern mit unvermindert hohem Wirkungsgrad und zusätzlich konstantem Netz Cos phi (0,98) gearbeitet wird.
Autoren
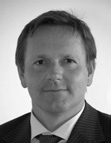
Frank Donsbach, Otto Junker GmbH Simmerath
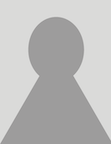
Steffen Niklaus, Otto Junker GmbH Simmerath
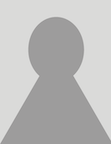